Personal Protective Equipment for Construction
- Posted on
- By Admin
- Posted in Personal Protective Equipment
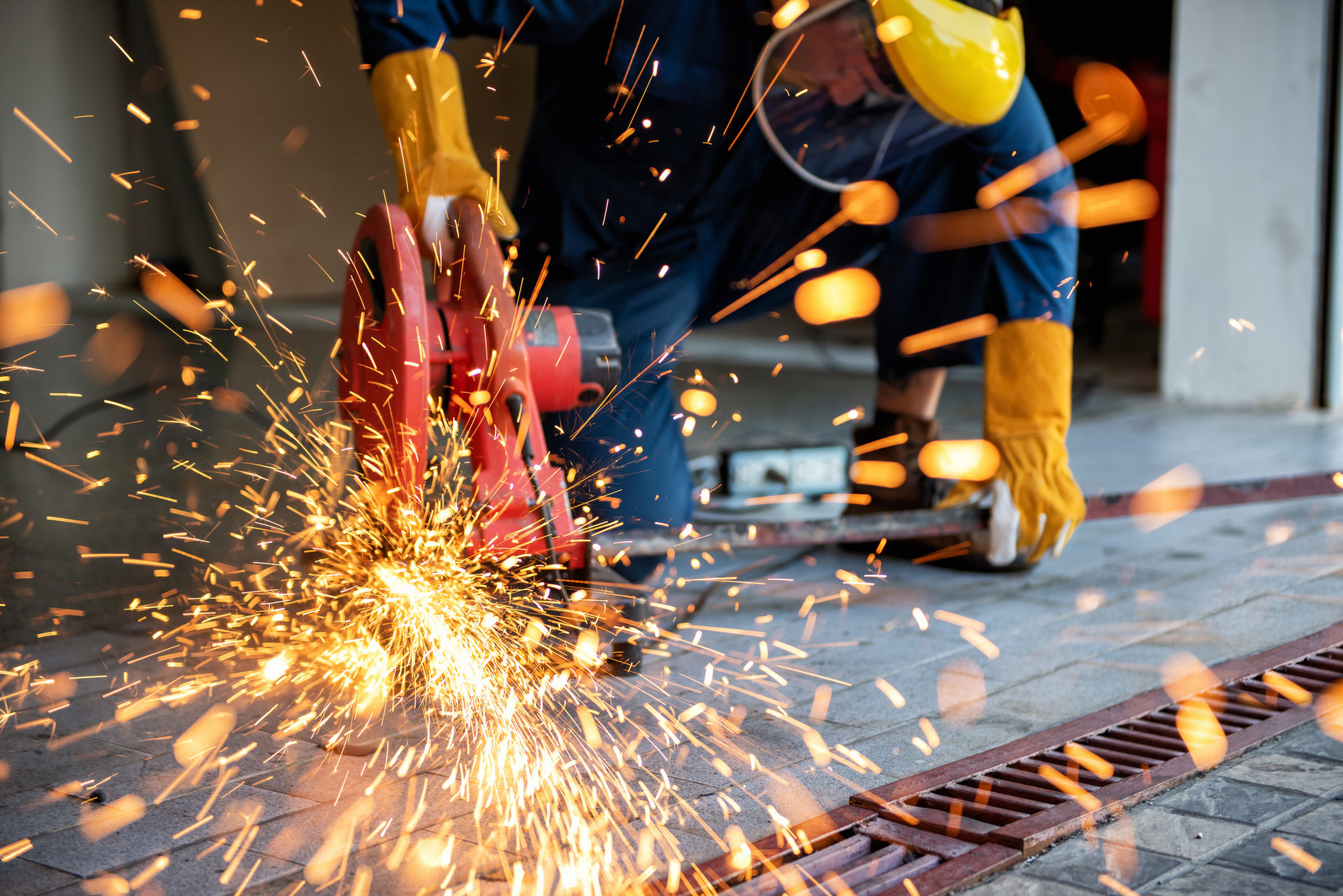
Personal Protective Equipment (PPE) is crucial in any business, but it's vital in the construction industry because of its numerous apparent risks. Construction companies should make sure that employees wear the correct PPE, regularly examine it, and insist on its use. PPE plays a vital role in ensuring safety for construction workers on the job. If preventative measures and safety control fail, PPE protects workers from injuries in the event of accidents.
Safety is a top priority for any worker. Unfortunately, the risk of accidents is extremely high within the construction industry because of the absence or lack of utilization of Personal Protective Equipment (PPE). PPE is a piece of equipment that safeguards workers from health or safety hazards on the job site and minimizes employees' exposure to dangers. The threats can range from slippery floors to falling debris. PPE can include eye protection, helmets, high-visibility clothing, footwear, safety harnesses, and respiratory protective equipment.
When you think of the daily uniform worn by construction workers, some of the things that immediately come to mind are safety glasses, a reflective vest, and the traditional hard hat. Although they may seem like an accessory to an outfit, they all are crucial to ensure work safety and are some of the primary items used in an individual's safety equipment. Personal protective gear is vital for safety on the job, so below, I'll provide you with the details of the purpose behind it, how it's needed and how you can utilize it to increase the safety of your employees.
Recently, PPE has been the subject of the spotlight since healthcare professionals depend on it to safeguard themselves from coronavirus and prevent their patients from contracting the virus and spreading the virus to other people. Yet, PPE has always been crucial in the construction sector, and training is an essential component of any formal PPE program. Employees need the training to operate the equipment and to be safe.
What is PPE?
It's no surprise that PPE usage safeguards from any dangers one might encounter while working, but what exactly is it? PPE refers to a broad term, personal protective equipment, used to describe equipment worn to safeguard the wearer from risks and dangers at the work location. While construction is among the most prominent industries that utilize PPE, other fields, including police, military, and firefighting, also use it.
Six Types of PPE
PPE is the acronym for Personal Protective Equipment used to refer to safety wear to protect wearers from injuries and accidents. The goal of this protective equipment isn't just for work but also for any activities related to sports and those that may cause harm to the body.
PPE minimizes the wearer's exposure to dangers through the act of an effective barrier. Therefore, properly-fitting personal protective gear is essential in various jobs and is congruent with OSHA standards. The different types of protective equipment include but are not limited to skin protection, eye protection, hearing protection, respiratory protection, helmets, head protection, protective clothing, and footwear.
1. Skin Protection. Chemical substances, biological agents, and physical agents are a few items from which your body requires protection. Agents like aerosols and radiation, extreme temperatures and parasites, and contaminated surfaces or splashes are hazardous and considered extremely risky that could cause permanent skin damage. The most common protective equipment for skin includes gloves and safety training, work boots, face shields, jackets, coats, and rubber aprons.
2. Eye Protection. Eye injury can occur because of large and small particles found in the air. Dust, broken glass, wood chips, sand, and cement chips are just a few of the causes of these types of injuries. Other injuries can include interaction with chemicals and other agents such as welding, light rays, etc. Safety glasses that have side shields, eye protection, and goggles are some of the equipment that protects eyes from injury.
3. Hearing Protection. Hearing issues are the most prevalent in the manufacturing sector, and the afflicted may not even notice they are suffering. It's a process that is unconsciously due to the noise levels that exceed the limit recommended by experts. The most common hearing protections are earmuffs or earplugs.
4. Respiratory Protection. is a means of being safe from inhaling toxic air that harms the body's respiratory system. There are two kinds of respirators: one is the gas mask specifically designed to remove harmful gases and chemicals. The other is an oxygen mask specifically designed to provide fresh breathing air.
5. Head Protection. The construction and the building industry most commonly use this form of equipment, consisting of safety helmets and caps.
6. Protective Clothing. This type of clothing is made from the most scientifically-tested materials to give maximum wearer security. Lab coats, high visibility garments such as ballistic vests, bodysuits, and work shoes are a few examples of this type of clothes. Employers must ensure that appropriate protective uniforms and equipment are available to employees in perfect working order.
The Importance of PPE
The construction industry is significant and is a crucial component of developing infrastructure that can give the country's economy the necessary boost. Recently the construction industry has seen tremendous growth. But unfortunately, many fatal accidents are reported in the construction industry each year.
For example, hazards at work cannot be avoided, particularly in construction, mining, and chemical labs. However, from an organizational standpoint, reducing risks by using PPE. PPE is equipment designed to safeguard the wearer and the user against hazards to health or safety that could arise while at work.
PPE includes safety helmets, gloves, footwear, harnesses, glasses, high-visibility clothing, and respiratory protection apparatuses. Each piece of PPE is composed of specially designed materials for its particular uses. PPE is categorized by what purpose it will fulfill and which part of the body needs protection. It is most effective when it has its user's proper size and fit.
Safety and health are an entire process consisting of workers in the workplace and supervisors, people in the vicinity, and managers. A competent site supervisor and efficient control of the activities are essential elements to ensuring safe and healthy conditions. Therefore, more risk control and management are necessary for construction work.
Three Leading Reasons for Construction Workers to Wear PPE:
1. Lesser Work-Related Injury. Each business should keep in mind that the loss of employees equals the loss of productivity; when a worker is injured, the company faces reduced work hours, lawsuits, workers' compensation premiums, and higher insurance costs. PPE, therefore, becomes a compulsory component of the workplace since one can't afford to suffer such disruptions.
2. Safety Aids in Enhancing Quality. Quality and safety are the same. The safety aspect can lead to safe workplace practices and greater effectiveness. Providing a safe and clean workplace makes it possible to ensure that workers focus on their work and minimize distractions. Thus, integrating PPE aids in boosting productivity and customer loyalty.
3. Greater Work Attendance. The loss of time caused by absences can significantly cost the bottom line. While employees may be injured or sick, they still need to be compensated, which results in lost profits and little productivity. PPE for construction and other dangerous work helps in reducing injuries and sickness and ensures greater profits.
PPE provides absolute protection for the worker if all other methods to reduce the risk are ineffective. An injury will happen if the PPE isn't present, which brings attention to the importance of PPE.
8 Regulations Covering Personal Protective Equipment
While PPE usage is vital in helping limit, minimize, or eliminate some dangers and risks associated with work-related actions and tasks, such equipment or clothes should be considered a last option.
If such PPE is considered essential, there is a clear danger. One should take all measures to reduce or eliminate this risk, including using PPE equipment only when a certain degree of risk persists regardless of other actions taken. The law requires employers to provide suitable PPE for all employees who need the equipment, with proper training and monitoring of the use of this equipment also being the employer's responsibility. There are eight specific areas employers must take close note of and ensure compliance.
1. The Provision of Personal Protective Equipment. When there is any indication of danger or risk for injury, the employer must provide suitable PPE equipment. All equipment or safety clothes offered must be ideal for the risks and conditions, be considered in light of the ergonomics requirements, fit correctly, aid in helping minimize or eliminate the risk, and conform to all CE specifications.
2. PPE Compatibility. Safety equipment and garments should be completely compatible with every possible combination of PPE equipment or clothing that might require wearing. For instance, eye protection shouldn't affect a breathing apparatus when worn together.
3. PPE Assessment. One must evaluate the features of the PPE to determine if it is suited to safeguard against the hazards involved. It is best to inspect the PPE against other options to ensure the most suitable choice. Also, re-evaluate any used safety gear to ensure it is still ideal for the environment, conditions, or dangers.
4. Maintenance of PPE Clothing and Equipment. The employer is accountable for regular maintenance and evaluation inspections to ensure that all safety apparel and equipment are still functioning, undamaged, and appropriate. Employers should implement procedures to ensure that an item or garment that fails to pass this test is removed from service and replacements immediately provided.
5. Storage of Personal Protective Equipment. The employer is accountable for providing appropriate and safe storage facilities for every PPE gear and apparel.
6. PPE Training. The employer is responsible for providing appropriate instruction and education about the dangers involved in the particular job, what PPE they can use to protect them, and how it is worn.
7. Use of PPE Clothing and Equipment. The employer's job is to ensure that all safety clothing and equipment are used correctly and properly maintained. Employees are accountable for using the equipment, following the instructions, and using the storage provided.
8. Reporting Defective PPE. The employer must implement the appropriate procedures and provide the proper training to ensure that employees are competent in conducting assessments of their equipment. Furthermore, if there is any malfunctioning, defective, damaged, or worn-out personal protective gear, workers should notify their manager.
If an employer fails to comply with these standards and an accident or injury should occur, they could be held legally accountable for damages. If an employer has doubts about selecting, maintaining, or using any PPE device, consulting with a reputable third party for the most up-to-date advice is recommended.
Why OSHA Requires Personal Protective Equipment
The number of accidents that occur at work is decreasing each day. Before, injuries were much more. These numbers have declined because of protective gear mandated by OSHA for workers to wear during labor.
Various workplace safety equipment is available to employees who work around hazardous chemicals or machines. For example, you may need safety glasses for your eyes or be required to wear respirator masks. These are only a few of the various types of protective gear that are available to protect you.
A lot of employees don't wear the equipment that is required. They can take advantage of the fact that an accident is not something that has ever happened to them. In many instances, they are the exact employees who suffer a devastating eye injury or lose their sight because of a workplace accident. If your job requires you to use any device, you have to be sure to wear it.
Chemicals are dangerous to an employee in various ways. OSHA has stringent guidelines that must be adhered to by all employees working with hazardous chemicals every day. Certain chemicals can trigger a myriad of health issues if handled in a way that is not safe. If you're working around any chemical, be aware of the OSHA guidelines for your workplace.
By adhering to the regulations set forth by OSHA, employees avoid many workplace accidents. In addition, if you wear the proper personal protective equipment, you are unlikely to be afflicted with a fatal or debilitating injury. Therefore, knowing OSHA's rules and regulations in your work environment is crucial.
PPE is more than just equipment that protects. There are three more crucial categories that are important, including respiratory protection, fall protection, and visibility. Falls are among the main reasons for death on construction sites; therefore, wearing suitable protective equipment like a safety harness is an excellent option to reduce the risk. The protection of the lungs is essential and using respirators to avoid inhalation of dangerous gases, vapors, and particles is another method to ensure that you are safe. Finally, your workers' visibility is essential when working on construction sites. Ensuring that you use high-visibility clothing makes workers easily identifiable and ensures that they can quickly locate anyone in an emergency.
The Risks Involved
Workers must wear PPE because of the numerous risks they encounter in the construction field. Workers expose themselves to various hazards based on the worksite, including being struck by electrical currents, falling, injuries to the head, and being trapped between objects. All of these could result in death under challenging situations. In addition, construction workers may suffer many serious and non-fatal injuries, including chemical burns, fractured bones, or severed fingers. Because of the seriousness of these hazards, businesses could face enormous fines for using safety equipment and, in some instances, be in deep legal trouble.
Improving Construction Site Safety
Safety on construction sites is a top priority for employers, so it is essential to follow safe procedures by using PPE. One way to execute this is to ensure your employees know how to utilize their equipment is pointing out what each piece of PPE can prevent and what it can't. In addition, PPE needs to fit correctly to ensure the highest protection, and proper maintenance and care are equally crucial in making sure you are taking safety precautions. Finally, it is also essential for workers to be aware of when to replace equipment, mainly if it is in contact with dangerous materials or is damaged, as it reduces its protective capacity.
Conclusion
Knowing why one should use PPE is crucial since huge fines, legal troubles, severe injuries, or even death can result from a lack of or incorrect use. In addition, personal protective equipment enhances the construction site's security. Thus, it is essential to create the safety of workers by ensuring proper testing and meeting all health and safety standards.
PPE is crucial in any business, but it's vital in the construction industry because of its numerous apparent risks. Construction companies should make sure that employees wear the correct PPE, regularly examine it, and insist on its use. PPE plays a vital role in ensuring safety for construction workers on the job. If preventative measures and safety control fail, PPE protects workers from injuries in the event of accidents.